The Future of Diesel Engine Piston Crown Design
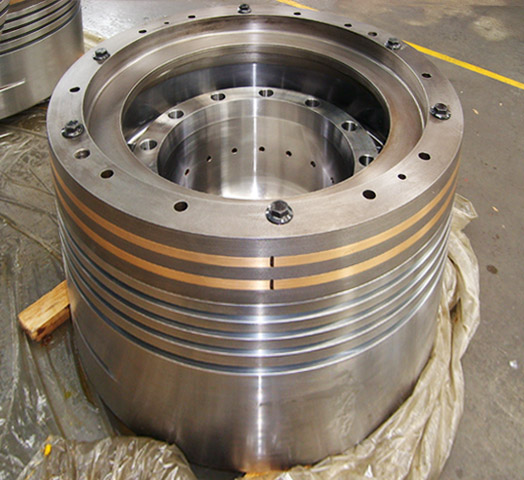
The diesel engine has been a cornerstone of industry for over a century. As with any technology, however, it is constantly evolving. One area of diesel engine design that has seen significant advances in recent years is the piston crown. Piston crowns play a critical role in engine performance, and their design can have a significant impact on fuel efficiency, emissions, and durability. In this article, we will discuss the future of diesel engine piston crown design and how it will impact the industry.
First, let’s start by understanding what a piston crown is and what it does. The piston crown is the top surface of the piston that comes into contact with the combustion gases in the engine. Its primary function is to transfer the energy generated by the combustion process to the connecting rod and ultimately to the crankshaft, which converts the linear motion of the pistons into rotary motion. In addition to this, it also helps to seal the combustion chamber and prevent gas leakage.
Traditionally, piston crowns have been made of cast iron due to its strength and durability. However, the increasing demand for improved fuel efficiency and reduced emissions has led to the development of new materials and designs. One such material is aluminum, which is lighter and has better thermal conductivity than cast iron. This allows for faster heat transfer from the combustion gases to the piston, resulting in better fuel efficiency and lower emissions.
Another trend in piston crown design is the use of bowl-shaped combustion chambers. This design allows for more efficient combustion by creating a vortex that helps to mix the fuel and air more thoroughly. The shape of the piston crown also plays a critical role in this process, as it helps to direct the flow of gases in the combustion chamber.
In addition to material and design changes, advancements in manufacturing technology have also had a significant impact on piston crown design. Computer-aided design (CAD) and computer numerical control (CNC) machining have enabled manufacturers to produce piston crowns with greater precision and accuracy than ever before. This has resulted in piston crowns that are not only more efficient but also more durable and reliable.
The future of diesel engine piston crown design is exciting, with many new developments on the horizon. One area that is likely to see significant growth is the use of composite materials. Composites are made by combining two or more materials to create a material with unique properties. They offer several advantages over traditional materials, including higher strength-to-weight ratios, better thermal conductivity, and improved wear resistance.
Another trend in piston crown design is the use of 3D printing technology. This allows manufacturers to create complex geometries and shapes that would be difficult or impossible to achieve with traditional manufacturing methods. 3D printing also allows for rapid prototyping, which can significantly reduce the time and cost involved in developing new piston crown designs.
The increasing use of electrification and hybridization in the automotive industry is also likely to have an impact on diesel engine piston crown design. As these technologies become more widespread, the demand for diesel engines may decrease, and manufacturers may shift their focus to other areas. However, diesel engines are likely to remain an important part of the industry for many years to come, and advancements in piston crown design will continue to play a critical role in their performance and efficiency.