Maximizing Diesel Crankshaft Life: 5 Proven Methods
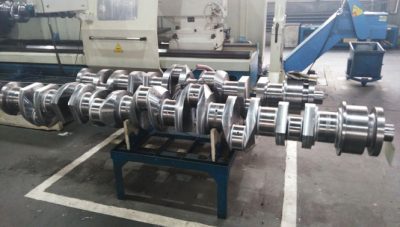
The Importance of Diesel Crankshaft Life
The diesel engine is a workhorse in the industrial sector, powering heavy machinery, transportation vehicles, and generators. The crankshaft, the heart of the engine, converts the reciprocating motion of the pistons into rotational motion, driving the transmission and other components. The durability and reliability of the diesel crankshaft are critical for the engine’s performance and productivity. In this article, we will discuss five proven methods to maximize diesel crankshaft life.
Method 1: Proper Lubrication and Maintenance
The proper lubrication and maintenance of the diesel engine are essential for the longevity of the crankshaft. The crankshaft and bearings require a constant supply of oil to reduce friction and wear. The oil should have the correct viscosity and additives to withstand high temperatures and pressures. A regular oil change and filter replacement schedule should be followed, and the oil pressure and temperature should be monitored regularly.
Method 2: Balancing and Dynamic Analysis
The diesel crankshaft’s balance and dynamic characteristics are crucial to prevent vibration, noise, and premature failure. The crankshaft must be balanced statically and dynamically to ensure that the mass distribution is uniform and the center of gravity is aligned with the rotation axis. The dynamic analysis evaluates the crankshaft’s natural frequencies, mode shapes, and critical speeds to avoid resonance and fatigue failure.
Method 3: Surface Hardening and Heat Treatment
The surface hardness and strength of the diesel crankshaft can be improved by surface hardening and heat treatment processes. The induction hardening, nitriding, and shot-peening are some of the methods used to increase the wear resistance, fatigue strength, and corrosion resistance of the crankshaft. The heat treatment processes, such as quenching and tempering, normalize, and annealing, can improve the mechanical properties and eliminate residual stresses.
Method 4: Material Selection and Design Optimization
The material selection and design optimization of the diesel crankshaft can significantly affect its life and performance. The material should have high strength, toughness, and fatigue resistance, such as forged steel, ductile iron, or titanium alloys. The design should consider the stress concentration, fillet radius, oil supply, and bearing clearance to minimize the stress and deformation. Computer-aided design and finite element analysis can help optimize the design and reduce the development time and cost.
Advancements in Diesel Crankshaft Technology
The advancements in diesel engine technology have led to the development of new materials, manufacturing processes, and design techniques that can further improve the diesel crankshaft’s life and performance. The use of advanced alloys, such as nickel-based superalloys, composites, and nanomaterials, can enhance the mechanical and thermal properties of the crankshaft. The additive manufacturing and create complex geometries and reduce the material waste. The digital twin and artificial intelligence can monitor the crankshaft’s condition, predict the failure, and optimize the maintenance schedule. By implementing these methods and technologies, the diesel crankshaft’s life can be maximized, reducing downtime, and increasing productivity